Fluoropolymer coatings can add the following significant properties to the surface on which they are applied.
– Heat resistance
– Chemical resistance
– Corrosion resistance
– Non-stick property
– Low friction
Services
Fluoropolymer Coating
The common Fluoropolymer coatings popularly used are : PTFE (most commonly known as Teflon), PFA, FEP, ECTFE (commonly known as Halar)

Mould Release Coating
(Rename of Decorative and Architectural coatings)
NON-STICK RELEASE COATINGS
When your application needs non-stick, low friction, dry lubricant or release properties
The key attributes of our fluoropolymer coatings include:
- Non-stick coating
- High temperature resistance
- Good abrasion resistance
VFM-ACS offers different PTFE (Xylan® & Teflon®) or Tungsten Disulfide (dry lubrication coating) coatings and solutions based on specific application requirements . It has outstanding release properties whilst also being very economical. This will directly improve production rates, minimise cycletime and reduce rejection costs.
KEY PROPERTIES
- Reduction in build-up
- Low Maintenance & Easy To Clean
- Improved Surface Finish
- Extends Life Span Of Mould Equipment
- Cost-Effective
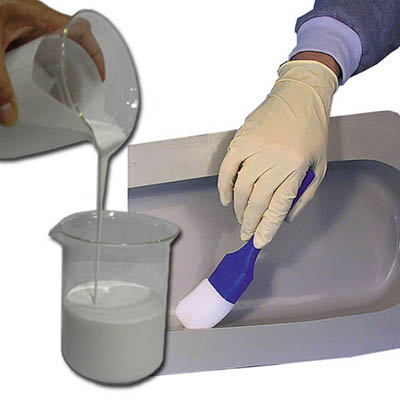
PTFE coating
Polytetrafluoroethylene (PTFE) belongs to fluorinated polymers and has excellent sliding and anti corrosive properties and is non-stick, water, heat and chemical resistant. This coating is commonly known as TEFLON coatings in the Indian market but actually TEFLON is the brand name of The Chemours Company.
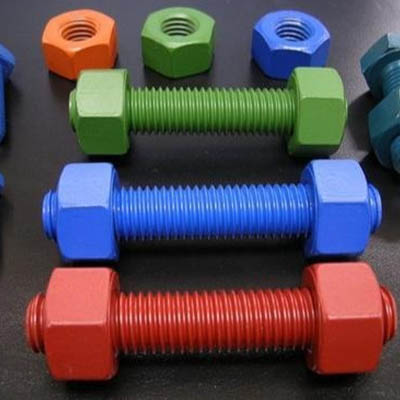
Xylan Coating
XYLAN is a trade name of thin film fluropolymer coatings from WHITFORD WORLDWIDE. XYLAN is a family of products designed to suit a wide range of applications.
- Used as a lubricant and wear resistant coating
- Used as a release or non stick coating
- Used in materials handling
- Used under conditions of corrosion
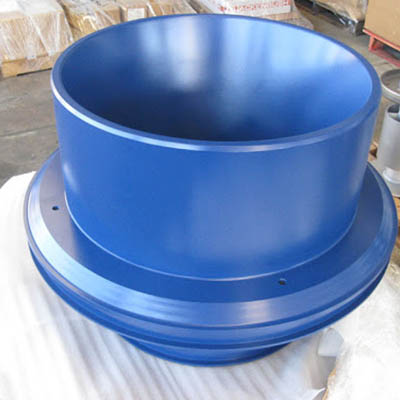
PFA / FEP coating
PFA is abbreviated as Perfluoroalkoxy Polymer Resin is a type of fluoropolymer with the properties almost similar to that of Polytetrafluoroethylene (PTFE). Perfluoroalkoxy alkanes (PFA) are used in high-temperature environments where absolute resistance and impermeability is required. Used in industrial, chemical, and food processing equipment, non-stick PFA coatings excel in high chemical resistance, non-adhesion, and health safety even at high temperatures. PFA coatings are also used on chemical vessels, piping systems, mixers, reactors, and many other devices.
FEP is abbreviated as Fluorinated Ethylene Propylene is a copolymer of hexafluoropropylene and tetrafluoroethylene. It is relatively a soft thermoplastic with lower tensile strength, wear resistance and creep resistance than any other engineering plastics. However, FEP coatings are chemically inert and have a low dielectric constant.

PEEK Coating
PEEK (polyetheretherketone) is a robust, rigid thermoplastic material. High-temperature plastic polymer polyetheretherketone (PEEK), can be used in the production of extremely resistant products and also as a surface treatment. It retains its physical properties even at very high temperatures and retains excellent bending and tensile strength. PEEK’s abrasion-resistant coating is suitable for use in the aerospace, automotive, health, etc. Because PEEK has superior chemical resistance – as well as resistance to steam and water, it is often used in applications where performance at elevated temperatures is required.
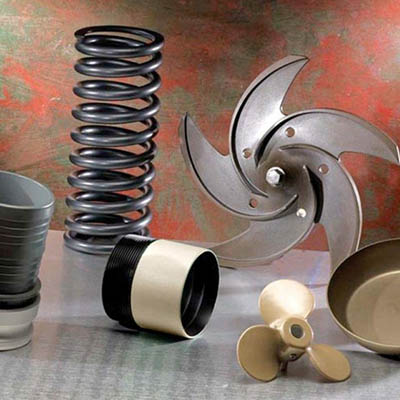
Nylon Coating
Nylon (polyamide) powder coating is widely used to protect a variety of metal substrates such as steel & aluminum. It is applied either electrostatically or in a fluid bed. It protects a wide variety of applications from corrosion to impact and abrasion. Nylon coatings are thermoplastic polyamide coatings and are under the category of ‘protective coatings’ in paints and coating nomenclature. Nylon has high dimensional stability, good resistance to stress cracking, and low moisture absorption. Nylon coating also has a low coefficient of friction and excellent abrasion resistance.
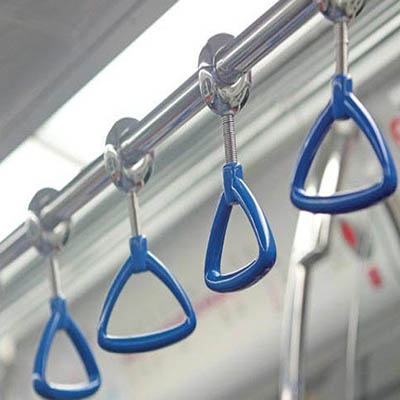
Epoxy & PU Coating
Epoxy Coatings: Epoxies have excellent adhesion to many substrates. They’re known for being “surface tolerant” which is why so many epoxy primers are specified. They can also be used as an intermediate coat and top coat due to their durability and impact resistance.
Polyurethane Coatings: Polyurethanes which is commonly referred to as PU coatings are known for their outstanding UV resistance, gloss retention and color stability. These coatings are usually sold as finish and are usually applied at 2-3 mils DFT.
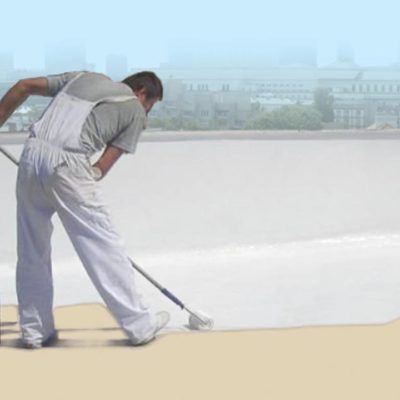
Halar Coating
Halar® is the registered trademark of ethylene chlorotrifluoroethylene (ECTFE), a chemical- and mechanical resistant plastic often used to coat both ferrous and non-ferrous metal substrates. . It is a fluorocarbon based fluoropolymer, a kind of plastic. Coating with Halar® provides mechanical resistance, long service life, and health safety. Halar® is characterized by its stability even at extremely low temperatures and is impact- and electric shock-resistant It provides high impact strength, chemical and corrosion resistance over a wide temperature range of -76˚C to 150˚C.
Coatings made from HALAR provide excellent chemical resistance and electrical properties to equipments that are operating at the temperatures up to 300℉. These are best suited for full vacuum applications. HALAR coatings are used to minimize wear in high frictional applications, where dimensional stability is a requirement. This coating is a machinable coating and can be machined to achieve the final required dimensions.
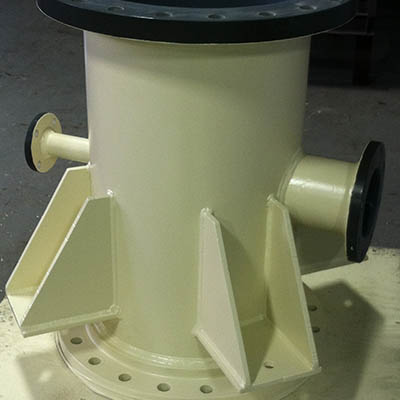